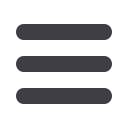

filters combined with dedicated water separators can be fitted on
the outlet of bulk tanks and mobile fuel carts to deliver clean water
free fuel from these tanks. It is important that filter and breather ele-
ments are replaced regularly and that water separators are main-
tained and drained when necessary.
The proper cleaning and draining of sludge and water from the
bulk tanks and mobile fuel carts are also important maintenance
tasks to ensure the cleanliness of fuel. Regularly check sludge levels
and rust in bulk tanks and mobile fuel carts and maintain accord-
ingly. It is recommended that the bulk fuel tank is installed at a slight
angle, with the drain plug at the lower point and the layout to the
pump at a higher point to keep debris and sludge in the bottom
of the bulk tank.
Ensure that the pump nozzle is kept clean and wiped off before fuel
is poured into equipment or mobile fuel carts. Regularly check all
hoses and connectors for leakages to prevent clutter from forming
due to dust accumulation. Fuel storage tanks and facilities should
also be properly secured to prevent unauthorised entry and tamper-
ing with the equipment, or theft of fuel – which may cause these
facilities and tanks to be filled up with foreign liquids.
Equally important is the maintenance on the engine-driven equip-
ment. Some best practices include to ensure equipment and fuel
tanks are filled up when they are stored to reduce the risk of con-
densation and water forming inside the tank. Never let new modern
engines run out of fuel or allow the fuel level to become too low.
The return fuel line from the new modern engine is hot and flows
directly back into the fuel tank. This can cause the temperature of
fuel to rise and damage the injector needles. Keep dust caps clean
from dust and debris and ensure it is properly sealed and closed off
to prevent dust particles from entering the system.
Also ensure fuel filters are replaced in accordance with the opera-
tor’s manuals and fuel standards, and drain water separators reg-
ularly. Trying to avoid operation of equipment at Peak RPM for
prolonged periods of time can result in better fuel economy and
reduced wear on key powertrain components.
Photo 4
is the result of a simplified test of fuel contamination on
a farm by means of which fuel is filtered through various different
kinds of filter media. It is evident that fuel contamination can in-
crease due to the improper handling of fuel on the farm.
Lubricity
To help with poor lubricity, there are special diesel fuel conditio-
ners that act as multi-functional fuel additive products for year-
round use to improve diesel fuel quality and maintain peak engine
efficiency and performance. Some of the features of the additive
include:
Boosting of the cetane number in fuel resulting in improved
ignition.
Improving the lubricity which can reduce wear of moveable
components.
Removing unwanted deposits and keeping the legacy mecha
nical fuel system clean.
Improving engine performance through better combustion.
Lowering of the cold filter plugging point, which results in better
fuel flow through the fuel filters.
Specific additives are also available for bulk fuel storage tanks and
are specially formulated to improve engine performance condi-
tions identified as injector sticking, engine misfire, rough idling, ex-
cess exhaust smoking, power loss and hard starting conditions in
modern high-pressure diesel fuel systems. In addition, special
equipment and additive solutions can be used to flush the engine’s
injector system to clean up internal injector deposits and debris.
Worn fuel injection components will result in poor combustion or
First sample
Fuel sample from storage tank without any
filtration system installed. Some high levels
of contamination were present.
Second sample
Fuel sample from the equipment's fuel tank
that was put in via a mobile fuel cart
without any filtration system. Increased
levels of contamination were observed
due to improper handling of the fuel.
Third sample
Fuel sample from the equipment after it
went through the equipment’s filtration
system. Not all contamination was removed
which resulted in excessive wear of the fuel
injection system that can lead to combus-
tion related failures of the engine.
4
over-fuelling that can result in expensive engine failures such as
piston damage, bearing damage and turbo failures.
Customers should consider doing regular fuel tests from bulk
and mobile fuel storage tanks as well as their engine-driven equip-
ment. Fuel samples should be taken in glass bottles or tin cans and
should be taken at the right levels.
Fuel tests like the IP440 or EN12662 are done to test for total fuel
contamination. Other important tests include sulphur content, ce-
tane number, density, flash point, cold filter plugging, viscosity,
and water content.
55
4: Fuel contamination test.